An e-liquid filling and capping machine is a piece of equipment used in the manufacturing and packaging of electronic cigarette liquids, also known as e-liquids or vape juices. These machines are designed to automate the process of filling bottles with e-liquid and sealing them with caps to ensure product quality, consistency, and efficiency. Here are some key features and components typically found in e-liquid filling and capping machines:
1. Filling Mechanism: These machines are equipped with a filling mechanism that accurately dispenses a predetermined amount of e-liquid into each bottle. Common filling methods include piston filling, peristaltic pumps, or gravity filling, depending on the viscosity and requirements of the e-liquid.
2. Nozzles: Filling machines are equipped with nozzles that ensure precise and drip-free dispensing of e-liquid into bottles. These nozzles can be designed to accommodate various bottle sizes and shapes.
When the bottle through the conveyor belt was sent to the location of the chuck, automatic identification of sensors, controlled by the internal program sent signals to the filling station, when the bottle came under the filling head, the cylinder head began to move down the drive filling, filling process without dripping, do not waste material, also can ensure the bottle clean and tidy, convenient after labeling.
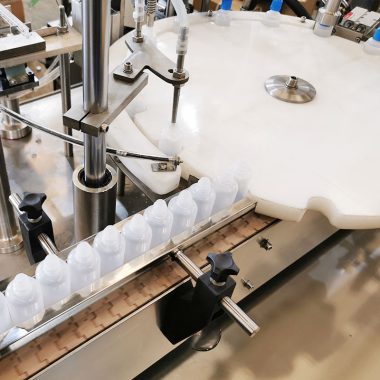
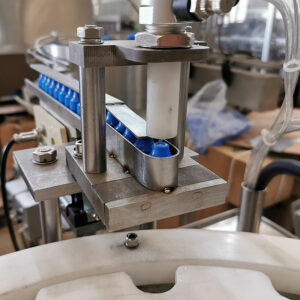
3. Cap Placement: After the e-liquid is dispensed into the bottles, a cap placement mechanism positions caps onto the bottle openings. This can involve screw-on caps or other types of closures depending on the packaging requirements.
4. Capping Mechanism: Capping machines have a capping mechanism that securely seals the bottles with caps. This can be achieved through different methods such as screw capping, snap capping, or crimp capping, depending on the type of caps used.
5. Conveyor System: E-liquid filling and capping machines are often integrated into a conveyor system that moves bottles through the different stages of the filling and capping process. Conveyor systems can be customized to accommodate various bottle shapes and sizes.
6. Quality Control: Some machines are equipped with quality control systems that inspect filled and capped bottles for defects, ensuring that only properly sealed and filled bottles are passed for packaging.
7. Adjustability: These machines are typically adjustable to accommodate different bottle sizes and e-liquid viscosities. Operators can configure the machine settings to meet specific production requirements.
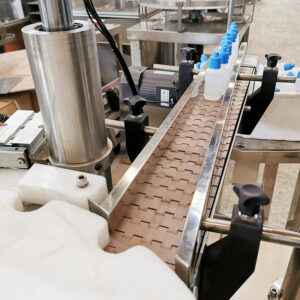
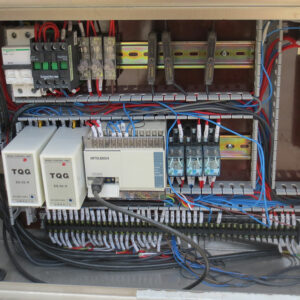
8. Hygiene and Cleanliness: E-liquid production requires a high level of cleanliness and hygiene to prevent contamination. Many machines are designed with features to facilitate easy cleaning and sanitation.
9. Automation and Controls: These machines are often equipped with programmable logic controllers (PLCs) and touchscreen interfaces that allow operators to set parameters, monitor the production process, and troubleshoot issues.
10. Output Rate: The output rate of these machines can vary widely, from small-scale machines suitable for small vape shops to high-speed production lines for larger manufacturers.
E-liquid filling and capping machines are essential for maintaining product consistency and efficiency in the e-liquid manufacturing process. They help reduce labor costs and minimize the risk of contamination, making them a valuable investment for e-liquid manufacturers of all sizes.